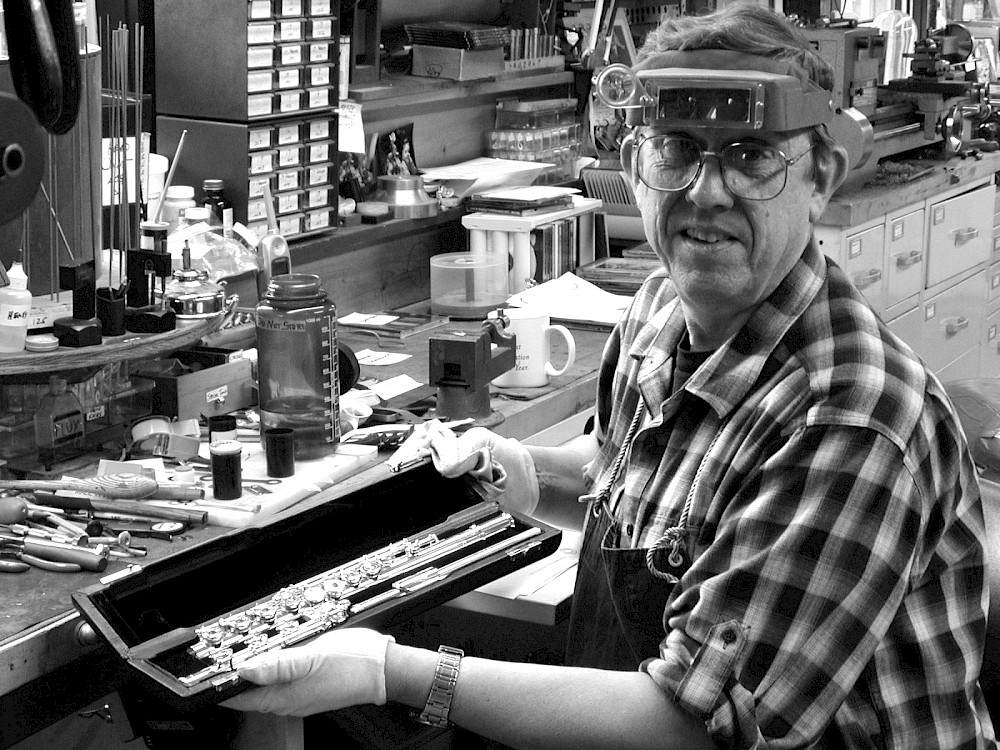
A fine flute should be maintained at least once a year by a qualified repair technician to allow the player to perform at their highest potential. The pads often swell or shrink due to humidity or temperature, and sometimes the skins become torn and leek instead of closing perfectly air tight. The changes that happen over time are very difficult for the player to detect because they happen very slowly and we can compensate for these problems sometimes by squeezing the keys. That extra finger pressure can hamper your ability to play smoothly and precisely at high speeds. It also can make the flute sound weaker and less resonant. The mechanism hinges need to have the oil changed every year to prevent the action from becoming slower and hesitant when returning to the open position.
Routine flute repair is called “Clean, Oil and Adjust”, because that’s the minimum amount of work to keep the flute playing as it should. The body is cleaned and most of the tarnish is removed. But major dents and scratches are left until it’s time for an overhaul with all new pads. The fitting of the foot and head tenon is usually tightened if needed.
Thinking back over a lifetime of working for professional flutists, it’s time to pause and review the possibilities that are not the usual things that most flutists would even imagine to be possible. Back in the early 1970’s I wanted to delve into the design possibilities of the head joint first, because it didn’t take as much time to build the tools for heads as it would take for building the entire instrument from scratch. At that time I don’t remember any other makers even offering to make head joints for the flute that were separate entities from the rest of the instrument. I had to convince people that the head joint is responsible for 80% of the actual tone qualities of their flutes, and that it makes a really significant difference to get the head joint that feels most comfortable and has the quickest response time. So the first few years in business I was concentrating on the needs of pro-flutists’ head joints. Thus the work to build the “Array”.
Key Extentions
I’ll never forget having a visit to my home workshop by Jeannie Baxtressor, principal flute of the NY Philharmonic, who was complaining about carpal tunnel wrist pains from practicing, rehearsing, performing and teaching so many hours per day. She had made little pieces of bone and extensions for some of the keys so she could hold the flute without cranking her wrists back in the manner of the “French School” teachers of that time. I had the time and the ability to make more permanent extensions that looked and felt more reliable on that Haynes flute she’d been playing since her college years. We struck up a wonderful friendship as a result, and she was very pleased with the extensions.
Several years later when I was teaching flute for private students and practicing regularly, I took a flute student who was an avid woodworker and played flute often for country dancing events. Tragically he had been injured when cutting wood on a table saw, because the board had suddenly jumped forward in the direction of the blade, and he lost the ends of three of the fingers of his left hand. Medical experts couldn’t restore his fingers after that accident, and he had gone to Elkhart to find someone who could help him to continue to play. He found a master flute maker there who had himself lost several digits while working in the machine shop, and he built a flute with extensions that would accommodate the injured left hand. But after playing that flute and bringing it to me for service, we saw that there was one small oversight in the design that made the left hand pads leak if he pushed down on the keys too hard. We decided to buy a used Haynes flute and make a similar key extension but would avoid the reliability issue when pressing too hard on those long extended left hand levers. I know he has been able to continue playing for his dance parties using that flute, and I do routine repairs for him annually.
One Piece Body and Foot
One of the drawbacks of the design of the modern flute is the very short tenon (telescoping connection) between the center joint and the foot joint. I’ve seen one possible solution to this problem where the flute maker used a longer tenon for the foot joint which had a hole to vent the D# tone hole when assembled to the body properly. I decided to try building the foot joint and the center joint both together on one single piece of tubing instead of trying to make them separate parts This meant that I needed a new fixture that would hold both the foot joint and center joint at the same time and string all the keys on this extra long flute body. I remember visiting the Library of Congress’ flute collection and seeing the gold flute that was made entirely in one piece including the foot joint and the center joint on one long tube. I found that flute to be extraordinary in all three registers, not just because it was made in a gold alloy, but the lowest notes were amazingly powerful and easy to control. So I set out to build a silver flute that would have a one piece body and foot, and made the head joint a separate part so the flute could be adjusted to the pitch of other players in the ensemble. The result was very rewarding! The lowest notes seemed to jump right out so much easier than the normal 3 piece flutes, because there is always a small amount of air leaking through that small tenon no matter how well it might be fitted. I’ve made three flutes with one piece bod and foot, and they are among the best flutes I’ve ever played. Low D comes out without any resistance, and the whole instrument vibrates in your hands when you’re playing. The only disadvantage to this design is the fact that you need a longer case for carrying the flute, but I have a wonderful case from England that makes this arrangement possible.
Customizing Flute Key Options
The C# Trill key has many technical features that most people aren’t even familiar with, because it’s not commonly included in a new flute commission. I won’t take the time to review them here, but suffice it to say we wouldn’t do without this key option regardless of the extra cost! Goodbye to that stuffy and SHARP C# note when you really need to play with a full sound that comes out perfectly tuned! (Griffes ‘Tone Poem’ for example). Most people would not know it is possible to add a C# Trill key to a finished flute if you know that’s something you really need. I can put the small extra balls on the 3 posts that hold the C# Trill key and string the new key on an existing flute without a problem. Silver plated flutes are off the table though. This is possible but more expensive than adding the key as an option to a new flute commission.
There is another C# key design by John Coltman that I have seen, but I haven’t built one yet either on a new flute or as a re-build to an existing flute. It should be possible, but I can’t say for sure just now.
Download Current Information Now!
Follow us
Contact us
Landell Flutes LLC
322 Main St, Wampum
PA 16157 USA
Phone (724) 740-1093
jonathon.landell@gmail.com
“There are over 180 handmade Landell flutes in silver and gold,
and one prototype flute in titanium. Innovation has been my hallmark.
Hard work has been the means.”
Jonathon A. Landell