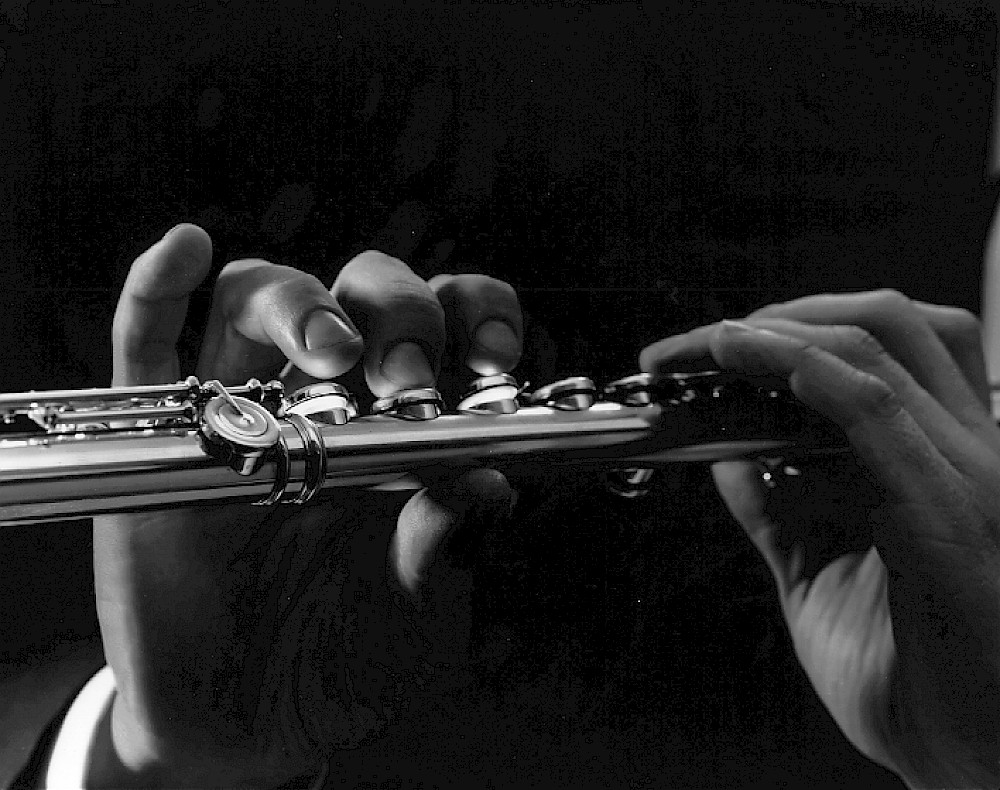
One of the remarkable things about fine handmade flutes is that they are made to be repaired, and so they will continue to play for hundreds of years if they are maintained regularly. Solid precious metal flutes will be around for many generations. Think of your flute as an ‘heirloom’ that will be a real treasure for people if it is cared for regularly and handled carefully. Here are some of the features of your modern Boehm flute that will help it thrive and survive for centuries.
1. Solid Metal or Plated
Solid silver or gold is durable like tableware or jewelry, and it can be easily re-polished or restored to its original luster by a craftsman. The metal is malleable (soft enough to stretch or be compressed) if there is a dent or scratch to the surface, and the body tube can be restored or re-sized to fit well into another instrument if necessary. But factory-made flutes are always plated with pure silver or gold which is so thin that it will wear off eventually. Plating may look pretty, but it adds nothing to the quality of the sound of the flute.
2. Tapered or Cylindrical Pivot Screws
The keys of the flute are mounted on hinges that provide accurate rotation for the pads, and the tapered pivots at each end give the ‘steels’ (hinge rods) a perfect rotation centerline, as long as they aren’t so worn that they move side-to- side. But factory-made flutes are often made with cylindrical pivots, which cannot be brought back into perfect rotational accuracy, because they cannot be tightened up like the tapered pivots can be.
3. Pins
Fine flutes are made with pins that are used to fix and align the movement of the ‘independent’ keys with the ‘dependent’ keys. These pins must be made carefully so the repair technician can remove them for cleaning and oiling the mechanism annually. Often the pins on factory-made flutes are almost impossible to remove without causing some damage to the key parts, because the production line will not allow the workers to take the extra time to fit them properly. It’s often necessary to replace the old pins with new ones.
4. Springs
The springs on handmade flutes use a 9k white gold alloy, because it has the most durable springing quality and can easily be adjusted to heavier or lighter pressure. Factory made flute springs use a bronze alloy that doesn’t last as long or give the possibility to change spring tension. It’s also much cheaper than gold
5. Pads
Many flutes are made with traditional felt pads which are wrapped with a bovine membrane called “Gold Beater’s skin”. These pads will need to be adjusted frequently because the felt material in the pad can swell or shrink with changes in atmospheric humidity, and the skin will become cracked and leak. Today we have several kinds of pads that use modern materials for the skin and the felt, which are more durable and stable.
6. Tone Holes
Today there are very few makers who build the flute bodies using soldered tone holes. In this design that was first used by Boehm, the tone holes are made from thick walled tubing and soft soldered to the extruded body tube. These tone holes sometimes develop a slight air leakage in the solder joint, and the repairer needs to be able to remove the offending tone hole and re-solder it to the body tube with fresh solder. The factory-made flutes are always made with tone holes that have been extruded by a machine directly from the body tube itself, so they cannot be removed or become un-soldered and leak.
But from a repair standpoint, if there is a serious dent that damages the “drawn” tone hole, it’s very difficult to repair that sort of damage. But with soldered tone holes, it’s possible to remove the tone hole and repair the dented tube, and then the tone hole can easily be re-soldered to the tube properly. Besides this advantage most well trained flutists have preferred the soldered tone hole design, because it has a more expressive range of sound than the drawn tone hole body of factory-made flutes.
7. Kicker Cork or Felt
‘Kickers’ are the small extensions at the back of many of the keys, which extend down to the body and control the size of the opening of the pad when they are not depressed. Most factory-flutes use a felt material on the ends of the Kickers. The reason many companies do this is to reduce the amount of ‘click’ that happens when the fingers release the keys to the open position. However, we have found that these small felts all become compressed over time due to the repeated contact.
We know that cork is a much better choice for the Kickers, because it doesn’t become compressed over time, which would cause the flute to play with a slightly higher pitch. It is obvious to most careful listeners that there is no real improvement in the amount of noise from felt Kickers compared with the sound of cork. We recommend using cork for all kickers except the Back Connection and the Bb Lever, where we always use felt.
8. Adjustment Screws or Clutches
The method that is commonly used to regulate the timing of the closure of the Dependent keys with the Independent keys is always controlled with very small adjustment screws, which are often hidden underneath the clutches in the keywork. The use of adjustment screws reduces the amount of time it takes to perfectly regulate the keywork, but these small screws often loose their accuracy due to wear or sloppy hand craftsmanship. The clutches of handmade flutes are more difficult to regulate during routine repairs, but they are far more stable and reliable over time.
9. Cases
The cases that are provided with “student” flutes are some of the worst protection for the instrument, but the “French” style case that is provided with most handmade flutes is not significantly more safe or reliable either. There have been better cases brought to the market recently, but the cost can be a burden to many flutists.
10. Head Cork or O-Ring
The head joint has always been made with a solid cork stopper above the embouchure hole, which is provided with an adjustable threaded rod that screws into the Crown. Some players need to be able to move the location of the cork slightly in order to improve their intonation in the third octave. There is no “perfect” location for the cork, even though that is usually assumed to be represented by the line placed near the end of the Swab Stick when held inside the head joint and up against the cork plate. But over time that Cork often becomes invaded by a green mold, which makes it impossible to move the cork at all. Now we have a design that uses O-Rings around a metal disk, which are absolutely air and water tight, so it will continue to function normally for years without fail.
11. Tenons
The three parts of the flute are fitted together tightly enough that there is no air leakage in the tenon and loosely enough that the parts can be assembled easily. Yet over time there is wear between these parts as we put the flute together to play and take them apart again. The problem is worst for the foot joint tenon, because it’s rather short and so it’s not very secure. This problem can be resolved by a competent repair person by swaging the tenon with a tool known as a burnisher, and sometime sanded smooth with very fine sandpaper strips.
It would be a very good idea to have the foot joint fitted very snug, and then carry the flute in a case that would accommodate the body and foot joint always assembled together. This would eliminate the wear and tear on the tenon from frequently assembling and disassembling the flute, and allow the foot joint to be fitted snug enough that it won’t leak any air. A new flute can be ordered from Landell Flutes that would build both the body and foot joint together on one continuous length of body tubing, which eliminates the problem of air leaking at the joint entirely.
12. Tarnish
The appearance of the silver flute is always impressive especially immediately after having been cleaned and polished. The black tarnish that occurs on any of the surfaces is unattractive because it looks ‘dirty’ to most people. Most flutists make it a habit to polish their flutes by hand frequently to prevent this tarnish from taking over. One problem with hand polishing the flute is the difficulty of avoiding touching the pads while polishing around the tone holes. In the long term it’s a futile battle with the elements, because the silver will always become tarnished anyway. By sending the flute to a repair person every year it’s possible to keep the tarnish from forming on the body of the flute, but it’s not possible to remove the tarnish from the keys without taking out all the pads.
But now there is a new patented alloy of sterling silver known as “Argentium Silver”, which was invented by British silversmith Mr. Peter Johns. Currently that alloy is not offered by the makers of silver and gold ‘Findings’, but we have been able to make enough flutes with Argentium to demonstrate the fact that this silver is just as suitable to professional flutists for tone and response, and the market for this alloy for flute making is yet to be developed. We hope that demand will slowly increase as more people become aware of it, and that the big companies which are able to make these products will step up to the plate and produce the materials that we want so much!
Download Current Information Now!
Follow us
Contact us
Landell Flutes LLC
322 Main St, Wampum
PA 16157 USA
Phone (724) 740-1093
jonathon.landell@gmail.com
“There are over 180 handmade Landell flutes in silver and gold,
and one prototype flute in titanium. Innovation has been my hallmark.
Hard work has been the means.”
Jonathon A. Landell